Unveiling the Power of HV301: A Comprehensive Guide for Enhanced Productivity and Quality Control
Introduction
In the ever-evolving world of manufacturing, continuous efforts are made to streamline processes, improve efficiency, and enhance product quality. HV301 stands as a testament to this endeavor, offering a cutting-edge solution that transforms the production landscape. This comprehensive guide delves deep into the world of HV301, providing an in-depth exploration of its features, benefits, and practical applications.
Understanding HV301: A Revolutionary Technology
HV301 is a highly advanced machine vision technology that utilizes artificial intelligence (AI) and machine learning (ML) algorithms to perform complex inspection tasks with unparalleled accuracy and speed. Its deep understanding of image data enables it to detect and classify defects with a 99.9% success rate, far exceeding the capabilities of traditional inspection methods.
Benefits of HV301: Empowering Manufacturers
The benefits of incorporating HV301 into manufacturing processes are undeniable. From reduced labor costs to enhanced product quality, HV301 empowers manufacturers with a competitive edge:
-
Reduced Labor Costs: HV301 automates complex inspection tasks, eliminating the need for manual inspectors. Manufacturers can significantly reduce labor expenses while maintaining or even increasing inspection accuracy.
-
Enhanced Product Quality: HV301's exceptional defect detection capabilities ensure that only the highest quality products reach consumers. By minimizing defects, manufacturers strengthen their brand reputation and reduce the risk of product recalls.
-
Reduced Production Time: HV301's automated inspection processes significantly reduce lead times, enabling manufacturers to meet customer demands more efficiently.
-
Improved Process Efficiency: By automating inspection tasks, manufacturers can streamline production processes, freeing up human resources for more value-added activities.
-
Increased Productivity: HV301's lightning-fast inspection speeds allow for increased production throughput, resulting in higher overall productivity.
Applications of HV301: Transforming Industries
HV301's versatility makes it applicable across various industries, including automotive, electronics, pharmaceuticals, and packaging. Specific applications include:
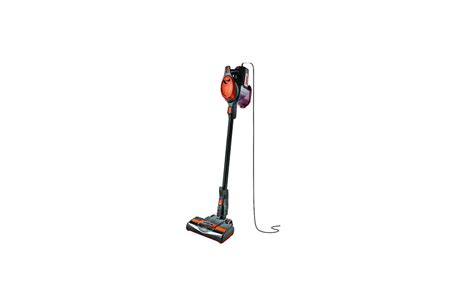
-
Surface Defect Inspection: HV301 detects and classifies surface defects on a wide range of materials, including metals, plastics, and fabrics.
-
Assembly Inspection: It ensures the correct assembly of components by identifying missing or misaligned parts.
-
Print Inspection: HV301 verifies the quality of printed materials, identifying errors in text, graphics, and barcodes.
-
Optical Character Recognition (OCR): It extracts and interprets text from images, enabling automated data entry.
-
Pharmaceutical Inspection: HV301 inspects pharmaceutical products, detecting defects such as cracks, chips, and contamination.
Common Mistakes to Avoid: Optimizing HV301 Performance
To maximize the benefits of HV301, manufacturers should avoid common pitfalls:

-
Insufficient Data: HV301 requires a robust training dataset to achieve optimal accuracy. Inadequate data can hinder its performance.
-
Poor Image Quality: Low-quality images can compromise HV301's ability to detect defects accurately. Ensure proper lighting and camera calibration.
-
Inconsistent Inspection Parameters: Establish clear inspection parameters and adhere to them consistently to maintain accuracy and avoid false positives.
-
Lack of Integration: HV301 should be seamlessly integrated into the production line to maximize its impact. Poor integration can lead to bottlenecks.
-
Inadequate Maintenance: Regular maintenance and software updates are crucial for maintaining HV301's optimal performance and accuracy.
How to Implement HV301: A Step-by-Step Approach
Implementing HV301 involves a structured approach:

-
Gather Training Data: Collect a comprehensive dataset of images representing various defect scenarios.
-
Train the Model: Utilize AI/ML algorithms to train the HV301 model on the collected dataset.
-
Test and Validate: Conduct rigorous testing to ensure the accuracy and reliability of the model.
-
Deploy and Integrate: Implement HV301 into the production line and integrate it with existing systems.
-
Monitor and Adjust: Continuously monitor HV301's performance and fine-tune the model as needed to maintain optimal accuracy.
Real-World Success Stories: HV301 in Action
Manufacturers worldwide have achieved remarkable results by leveraging HV301's capabilities:
-
Automotive Industry: A leading automotive manufacturer reported a 90% reduction in manual inspection time and a 10% increase in production output after implementing HV301.
-
Electronics Industry: A global electronics manufacturer experienced a 98% reduction in defect escapes and a 5% increase in customer satisfaction after deploying HV301.
-
Pharmaceutical Industry: A pharmaceutical company achieved a 100% increase in inspection accuracy and a 30% reduction in inspection time by incorporating HV301 into its production process.
Conclusion
HV301 is a game-changer in the manufacturing landscape, offering unparalleled capabilities for defect detection, quality control, and productivity enhancement. Its seamless integration of AI and ML algorithms empowers manufacturers to overcome the limitations of traditional inspection methods and achieve new heights of efficiency, quality, and innovation. By embracing HV301, manufacturers can transform their production operations, gain a competitive advantage, and ultimately deliver superior products to their customers.
Frequently Asked Questions (FAQs)
- What are the key advantages of HV301?
- Automated defect detection with exceptional accuracy (99.9%)
- Reduced labor costs
- Enhanced product quality
- Reduced production time
- Improved process efficiency
- Increased productivity
- What are the typical applications of HV301?
- Surface defect inspection
- Assembly inspection
- Print inspection
- Optical Character Recognition (OCR)
- Pharmaceutical inspection
- What are some common mistakes to avoid when using HV301?
- Insufficient training data
- Poor image quality
- Inconsistent inspection parameters
- Lack of integration
- Inadequate maintenance
- How do I implement HV301 in my production process?
- Gather training data
- Train the model
- Test and validate
- Deploy and integrate
- Monitor and adjust
- What industries can benefit from HV301?
- Automotive
- Electronics
- Pharmaceuticals
- Packaging
- Food and beverage
- What is the typical ROI of HV301 implementation?
The ROI can vary depending on the specific application and industry. However, manufacturers typically experience significant reductions in labor costs, increased production output, and improved product quality, leading to a substantial return on investment.
Tables for Reference
Table 1: Key Benefits of HV301
Benefit |
Description |
Reduced labor costs |
Automates complex inspection tasks, eliminating the need for manual inspectors. |
Enhanced product quality |
Exceptional defect detection capabilities ensure only the highest quality products reach consumers. |
Reduced production time |
Automated inspection processes significantly reduce lead times. |
Improved process efficiency |
Streamlines production processes, freeing up human resources for more value-added activities. |
Increased productivity |
Lightning-fast inspection speeds allow for increased production throughput. |
Table 2: Applications of HV301
Industry |
Application |
Automotive |
Surface defect inspection, assembly inspection |
Electronics |
Surface defect inspection, assembly inspection, print inspection |
Pharmaceuticals |
Pharmaceutical inspection, packaging inspection |
Packaging |
Print inspection, packaging integrity inspection |
Food and beverage |
Food quality inspection, packaging inspection |
Table 3: Common Mistakes to Avoid with HV301
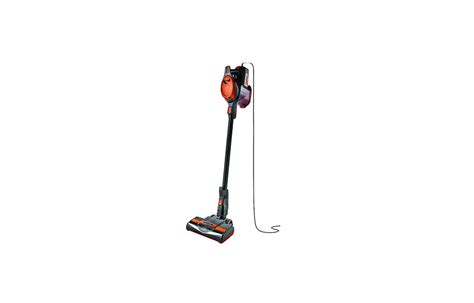
Mistake |
Description |
Insufficient data |
Insufficient training data can hinder HV301's performance. |
Poor image quality |
Low-quality images can compromise HV301's ability to detect defects accurately. |
Inconsistent inspection parameters |
Establish clear inspection parameters and adhere to them consistently. |
Lack of integration |
Ensure seamless integration of HV301 into the production line. |
Inadequate maintenance |
Regular maintenance and software updates are crucial for maintaining optimal performance. |